5 - HTM log purlin cold-vented roof SIPS design tips
Passive solar roof details do not have to be unique, but cold vented roof design with vented SIPS panels and layered insulation is a natural with log purlins. A lot of attention has been given to our passive solar house plan choice of log roof beams purlins, but you can certainly use dimensional lumber and trusses in your roof details if you wish. Square timbers are easier to build with than trying to use round logs. The main advantages to log purlins are in their availability since you may have to drop trees to create your home site and their cost since raw logs are cheaper and always more environmentally sound than processed lumber. But what you notice after the home is finished is the way the round logs greatly soften the angular nature of an HTM. They truly add a great deal of beauty to the final product and are a natural choice for a flat roof deck.
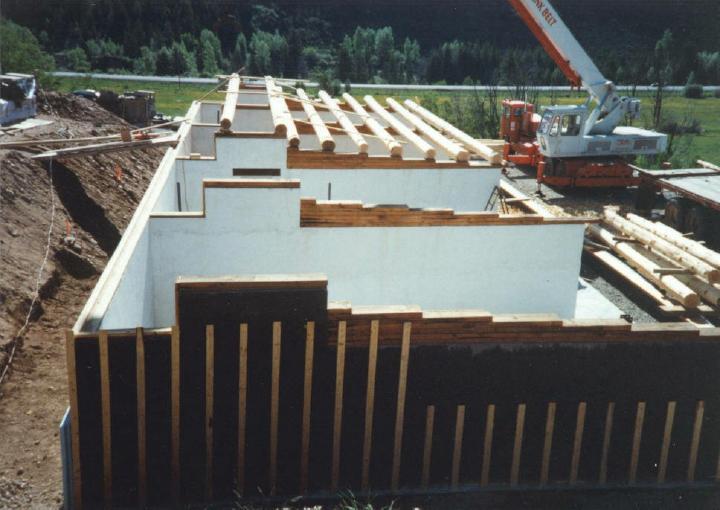
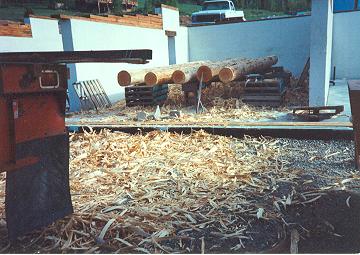
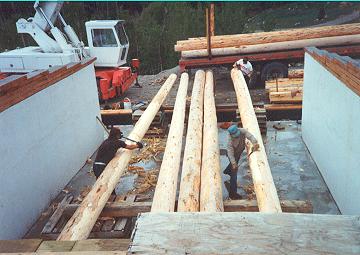
There is no 'one best way' to build any structure in any one climate and or soil type. As with any design question, the answers vary from project to project and need to be addressed in a more holistic manner to function properly. You can build your own roof panels, as shown below, sandwiching EPS blueboard atop the ceiling planks. Or you can order the SIPS panels readymade. It all boils down to initial cost versus labor time savings. Insulated structural roof panels SIPS are a great way to save time during construction. Get a quote on vented SIPS panels locally to compare cost. Sometimes the quality is good and the engineering they provide very helpful. Look for R30 minimum and extruded EPS blueboard or the newer generation expanded insulation boards, not white Styrofoam® bead board, since it absorbs water more readily.
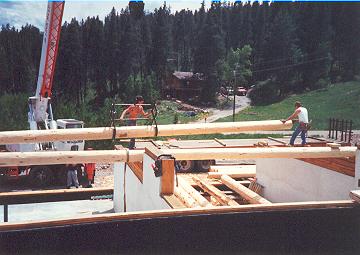
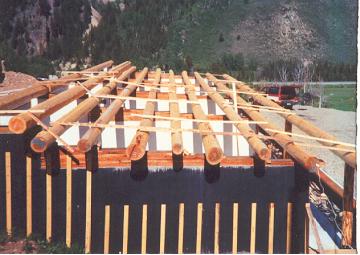
SIPS panels come with faux finishes on the ceiling side, sometimes perfectly imitating tongue and groove or stucco. Always go with the cold vented roof option. 'Cold roofs' are a design that will cut your cooling bills dramatically by allowing heated air to vent out the roof peak. Using a layer of Mylar® reflectix atop the felt in a cold roof design is a recommended to most designs and climates. This Mylar layer gives your roof the advantage of reflecting heat back up and not absorbing into the insulation underneath. We have found this system to have a great many benefits. The beauty is hard to argue with. With so much stone, block, and stucco, the use of wood on the ceiling to soften the look is a design imperative. This choice of material is also more natural and healthier than drywall. Drywall ceilings are so very sterile and, well, just so very white. Think twice before you commit to that type of ceiling construction.
HTM designs concentrate on simplicity and ease of construction for the homeowner-builder. Deck roofs fit this need. As you can see in these photos, construction simply consists of building a box and filling it with EPS foam sheets. There are several design details not shown here, like the moisture barrier between the foam and the decking, but the basics are evident. You can see where attention is given to overlapping joints and caulking gaps. Note this is a vented, 'cold roof' design with the plywood sheeting laid upon the 2by4 sleepers atop the final layer of foam. This allows the roof to vent, preventing overheating and ice dams. Vented, cold roofs are very important in both hot and cold climates. You can't afford to allow heat buildup in your roof to penetrate into the home. Always design with a vented, cold roof to protect decking from water damage.
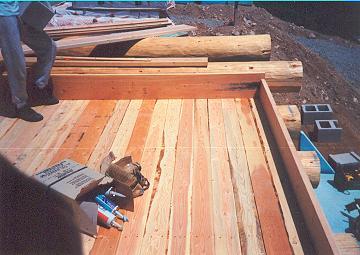
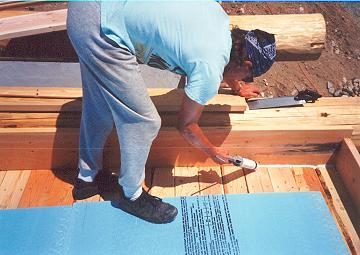
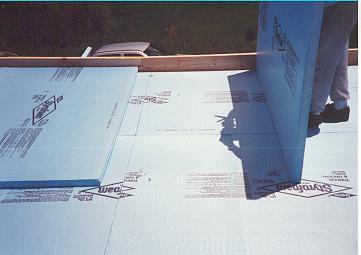
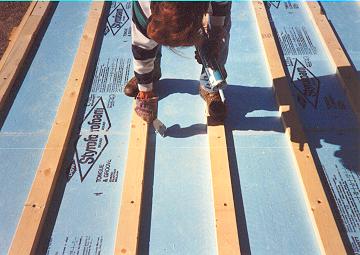
As with any aspect of building, there are dozens of ways to approach the construction. The following two sketches are two of the most common methods to construct a cold, vented roof. Pre-built insulated roofing panels are certainly another option and the extra expense is sometimes worth the savings in labor. For most clients, the 'sandwich' style is easier to construct with minimal skills. The conventional joist approach shown above is often more popular with contractors who wish to use fiberglass batting insulation.
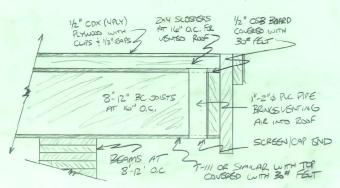
The ceiling planking shown below is classic penny pinching. As the 2by6 tongue and groove ceiling planks neared the peak of roof, we ran out of product. The last 10 T&G boards are actually 2by12 planks we notched with a router to mock the look of T&G grooves. Give it a close look and you will see the change in planking material about half way up. Curiously enough, the tongue and groove does not add strength to the deck - it just keeps the boards from wanking and warping as they dry. If you use well-seasoned 2by12 lumber, you can plane 45 degrees off both sides of the plank and router Vee cut the middle for much the same structural and visual effect, at a pretty healthy savings.
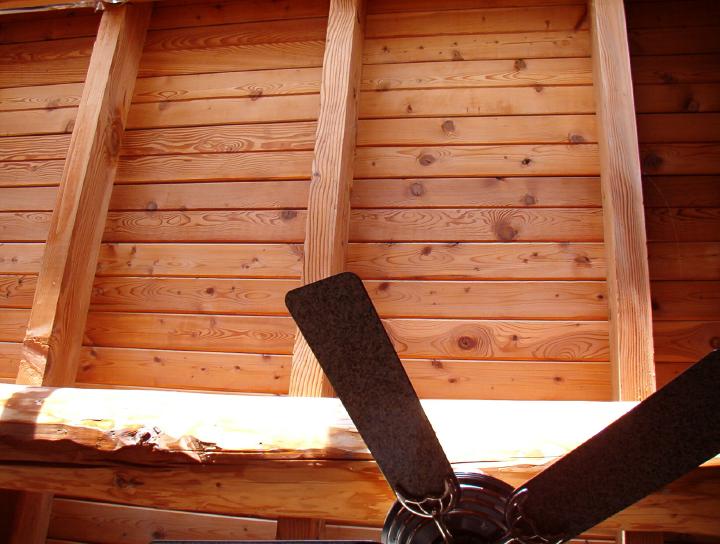
With any home roof design, it is key to note:
Metal roofing has its strong points, but there are negative aspects. It is attached with screws. When you nail through bitumen underlayment (Grace), it seals around the spike. When you screw through it, though, the boring action of the screw causes it not to seal around the threads. Metal roofs also tend to expand and contract. You will be up there with a screw gun tightening them every 3 or 4 years unless you install a standing seam design, which is expensive, but a good investment. Eventually the screws will not tighten as they have eaten out the hole and you will have to install all new, fatter screws. Another detraction is that the color will fade on all but the most expensive metal roofs. They use high grade automobile paint on most brands. Another will actually change color as you walk around it looking from different sun angles. Others are designed to rust up to a point and then they stop, which is a nice look. Metal roofs are not fireproof. For the same cost as mid-price standing seam with hidden fasteners, you can get the best shingles which in practice are much more fireproof. You could start a campfire on a 540# shingle roof and it will eventually burn a hole through the roof and fall inside, maybe going out or at least being easier to fight. Start the same campfire on a metal roof and it will heat the metal, eventually flash firing the entire roof.
HTM Passive Solar eBook – Table of Contents
- introduction to high thermal mass pragmatic design, low-tech functions, and materials
- photo gallery is packed with images, commentary, and our free HTM Home Tour video
- dry stack surface bonding cement construction photos and some block layout sketches
- floor plans features several functional basic layouts and commentary on design choice
- roof detail chapter with T&G plank-style vented roof decking atop log purlin joist beams
- sun screens critical passive solar design component to create favorable micro-climates
- heat storage fiberglass water tanks are a low-tech way to moderate temperature swings
- earth tubing is simple passive technique to temper a household’s fresh air return intake
- solar orientation isn’t critical since HTM designs excel in hot or cold climates anywhere
- exterior fascia SBC coatings over EPS foam board insulation and sloped glazing details
- wing insulation and shallow footer, frost-protected perimeter foundation design choices
- planter beds are a central, functional component of greenhouse-style HTM construction
- links page is filled with a helpful selection of research references and relevant websites